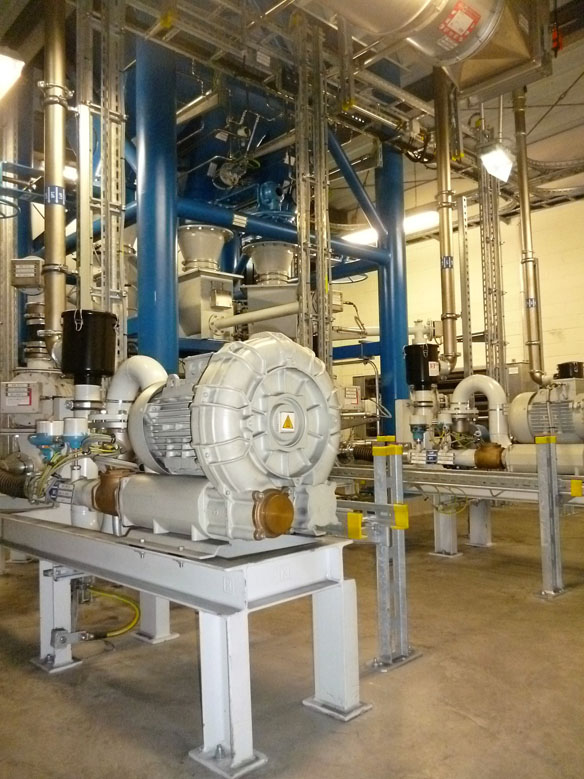
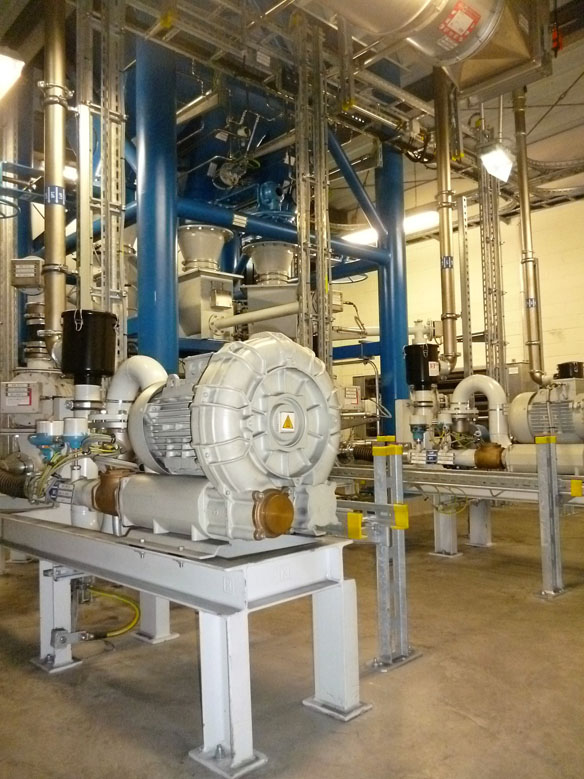
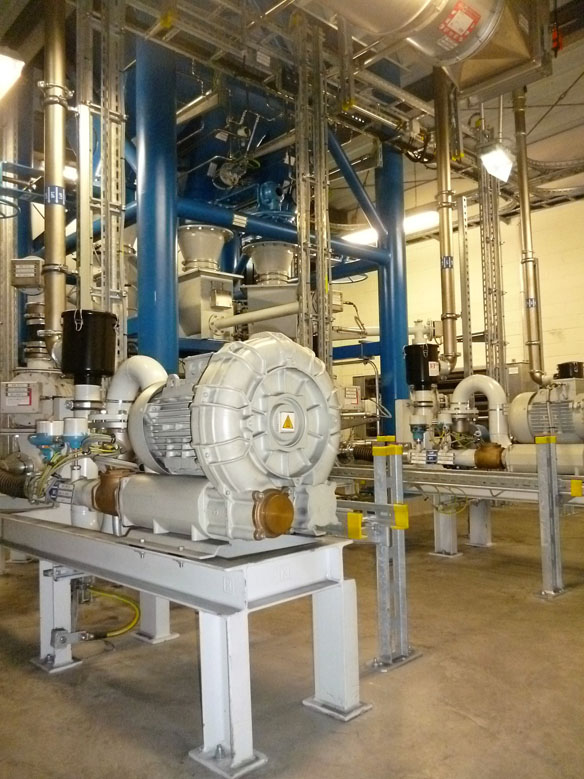
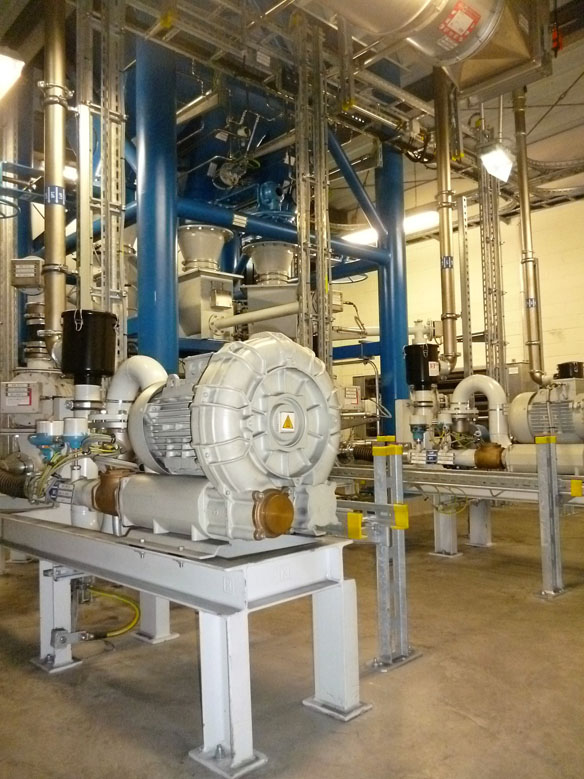
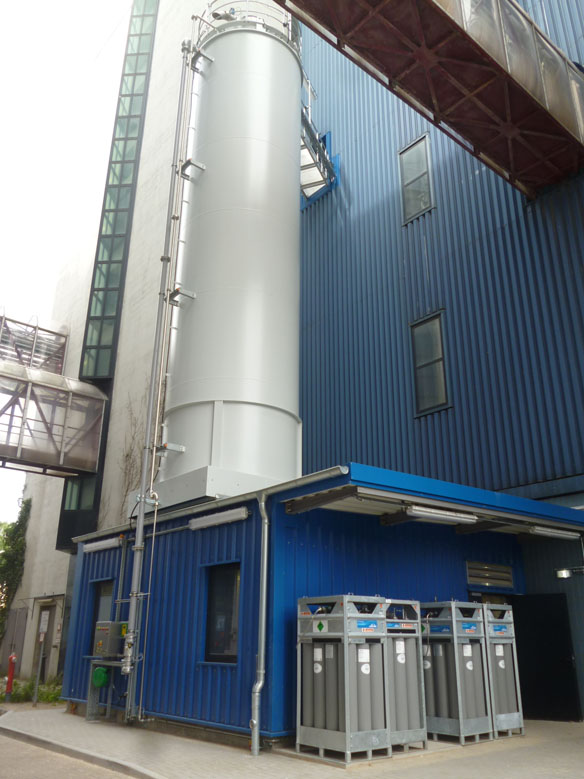
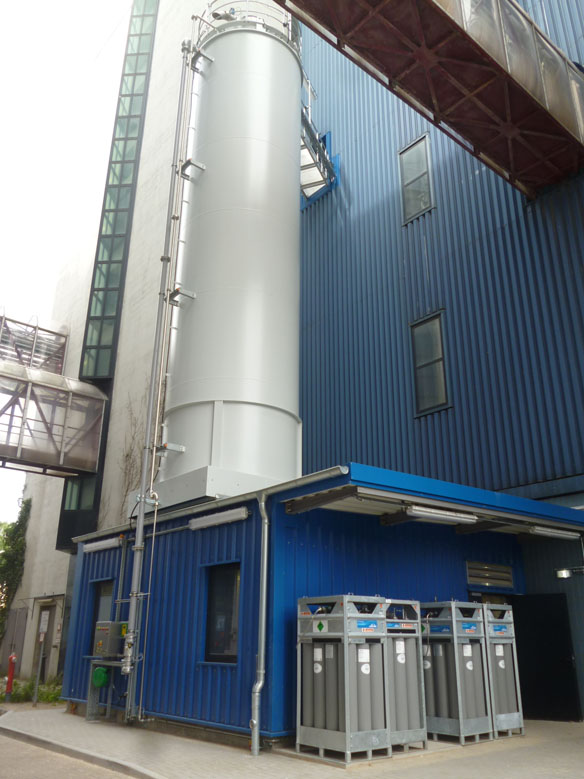
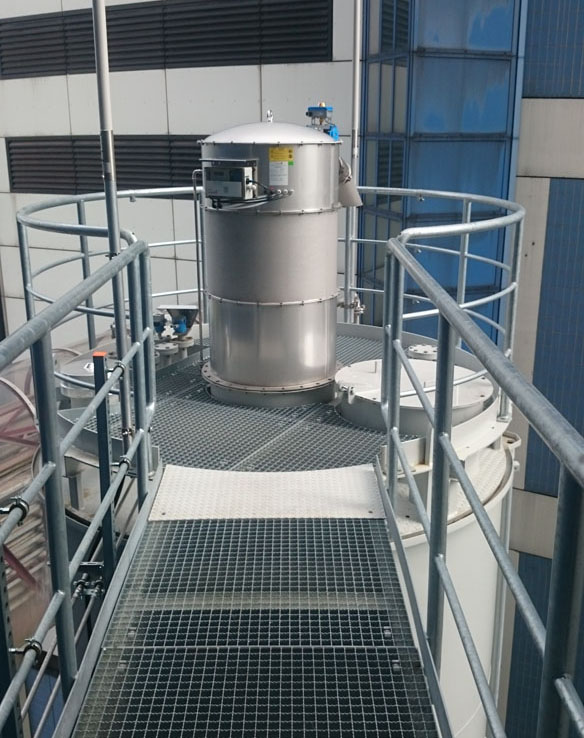
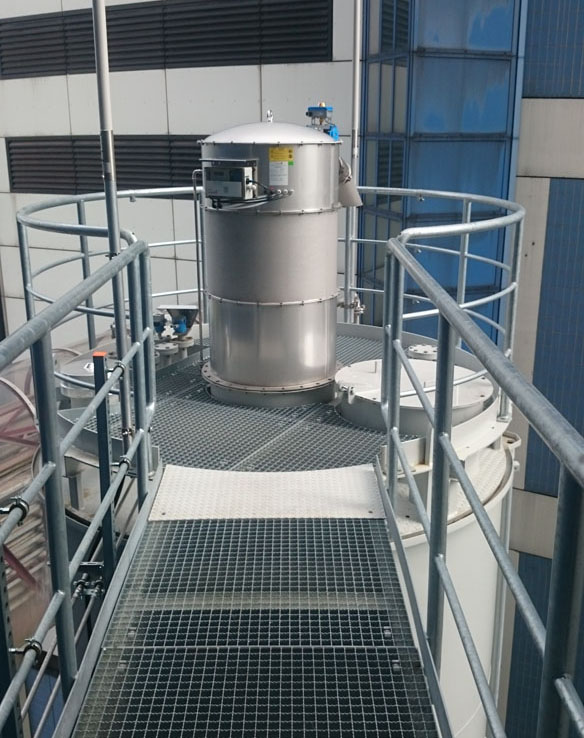
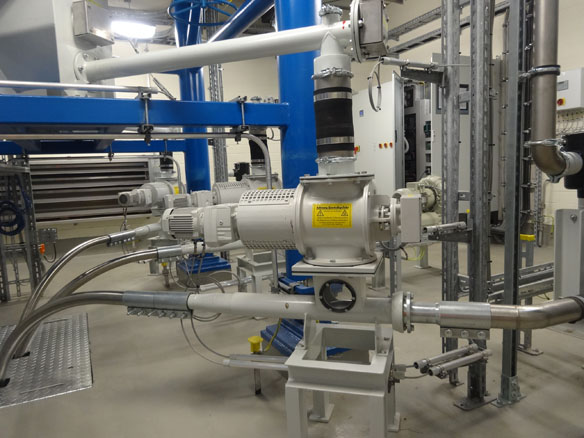
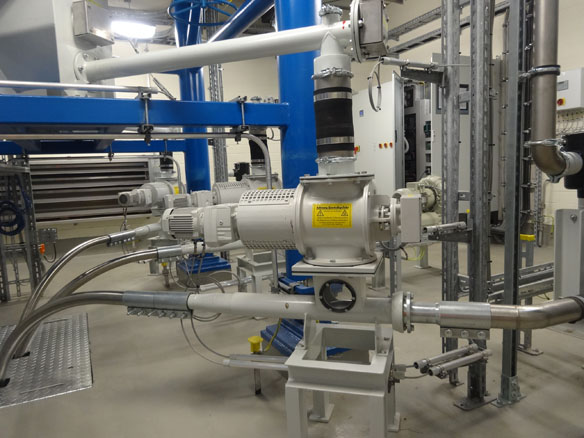
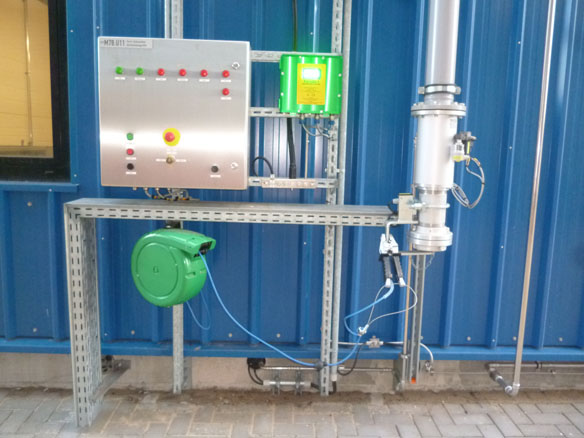
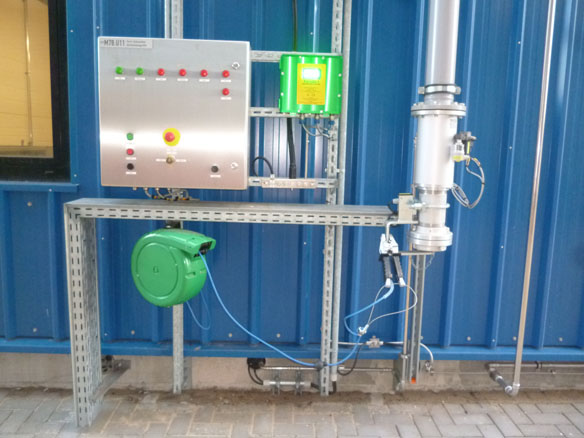
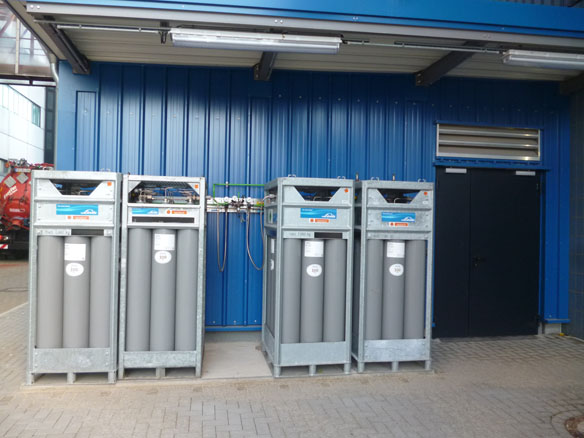
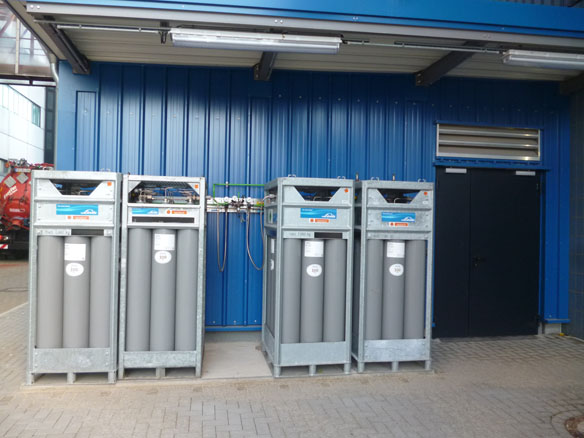
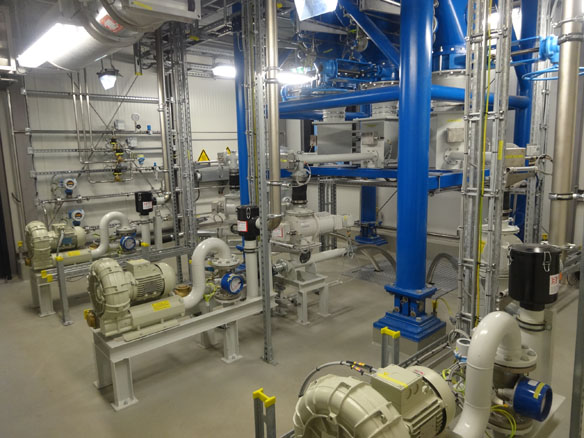
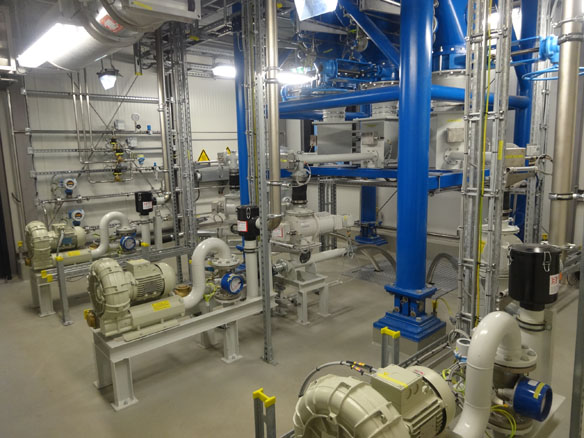
Activated carbon metering on a large scale
An important additive is grinding activated brown coal (activated carbon). This binds any mercury and other substances in the flue gas, which can then be separated by fabric filters. In order to ensure that activated carbon is fed into the flue gas in a targeted and tailored manner at the touch of a button, IB Verfahrens- und Anlagentechnik delivered a silo system with downstream single metering for four combustion lines. The metering lines can be operated individually, as well as simultaneously and completely independently of each other.
Special features at a glance
- Storage silo with pneumatic filling
- Silo top-mounted filter for surge air
- Continuous fill level measurement
- Silo ventilation to support discharge
- Low-pressure injector sluices for thin stream conveying
- Metering from 1.5 to 15 kg/h per line (3)
- Rendering the storage silo inert
- Rendering the silo inert if
Description
The system comprises the following main components: storage silo with filling system, metering and pneumatic conveyance. Activated carbon is provided by a silo vehicle. The storage silo is filled using compressed air generated by the silo vehicle’s on-board compressor. To do this, excess pressure is established in the silo vehicle’s tank, which blasts the activated carbon into the storage silo via the filling line that is connected. Any surge air that occurs is cleaned by the silo’s top-mounted filter and discharged into the atmosphere.
The storage silo has a continuous fill level measurement system, as well as MAX and MIN sensors. These provide the control technology with information regarding the available quantity of activated carbon in the storage silo at all times. Furthermore, corresponding sensors are used to record the pressure ratios and the temperature. The storage silo’s four outlets are equipped with pneumatic loosening equipment. This prevents bridging in the product and ensures that the activated carbon can be removed properly by the four metering units arranged below.
Rotary feeders that were developed especially for the application situation are used as metering devices. These meter the requested quantity of activated carbon into low-pressure injector sluices arranged underneath. The quantity is controlled by adjusting the frequency on the drive for the corresponding rotary feeder. The metering quantity is specified by the control technology. The metering range is from 1.5 to 15 kg/h per line.
The metered quantity of activated carbon enters a corresponding low-pressure injector below the rotary feeders. This is pressurised by the pressurisation fan or the compressed air infeed with conveying air. The metered quantity of activated carbon is now injected into the conveying air. The pipeline system is used to convey the activated carbon by thin stream conveying towards the corresponding flue gas duct. The furthest distance is around 100m, whereby a height of around 33m must be overcome. A corresponding lance is used for injection into the flue gas duct, which ensures homogeneous distribution of the activated carbon in the flue gas. The actual process of adsorbing the harmful materials starts from here and ends when it is separated in the fabric filter.
The complete system is rated as potentially explosive based on an expert report. As a result, the design is protected against explosion according to the applicable ATEX regulation 94/9/EC (ATEX100a). The measures taken correspond to the report’s zone distribution and must be adhered to consistently. They include the use of components with the suitable Ex approval and marking, the use of conductive or dissipative materials, temperature monitoring at different points in the storage silo, MAX fill level monitoring, the complete potential equalisation between the components and the connection to the building earth.
In order to fight fires or hot spots that have entered, a system to render the storage silo inert via the pneumatic loosening equipment is provided. If required, the loosening system can be operated with nitrogen instead of with compressed air. If the storage silo has to be emptied despite this, the connection can be used to empty the storage silo in a controlled manner via a corresponding emergency discharge chute. The complete system has been checked by a qualified person and accepted successfully.